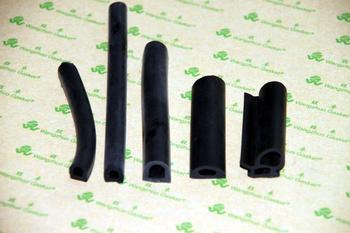
The sealing material can be formulated into a liquid or paste during use, applied between the contact surfaces of the two parts, and cured under certain conditions or with a non-dry putty to seal; it can also be processed into various shapes of solid or Hollow rings are installed between the contact surfaces of the two parts to seal. The former claims that the sealing material is only used for the static sealing parts where the contact surfaces of the two parts do not move relative to each other; the latter means that the sealing parts can be used not only for static sealing parts but also for dynamic sealing parts where the contact surfaces of the two parts move relative to each other.
Sealing materials used in the aerospace industry include polysulfide rubber, silicone rubber, and polyurethane sealants. Polysulfide rubber sealant has excellent resistance to aviation fuel, and is mainly used for the sealing of the wing and fuselage integral fuel tank. Silicone rubber sealant can withstand high temperature and low temperature, radiation resistance, vacuum resistance, non-pollution, non-toxic, and is mainly used for the sealing of various seal chambers. Polyurethane sealants have good ultra-low temperature performance and are mainly used for liquid hydrogen and liquid oxygen joints of rocket propellants. Encapsulants are also used to seal the cockpit, window doors, instrumentation bays, artillery bays, ejectors, electrical plugs, electronic components and electromagnets.
Sealing materials are metal materials (aluminum, lead, indium, stainless steel, etc.), non-metallic materials (rubber, plastics, ceramics, graphite, etc.) and composite materials (such as rubber-asbestos board), but the most used is rubber elasticity. Body material.